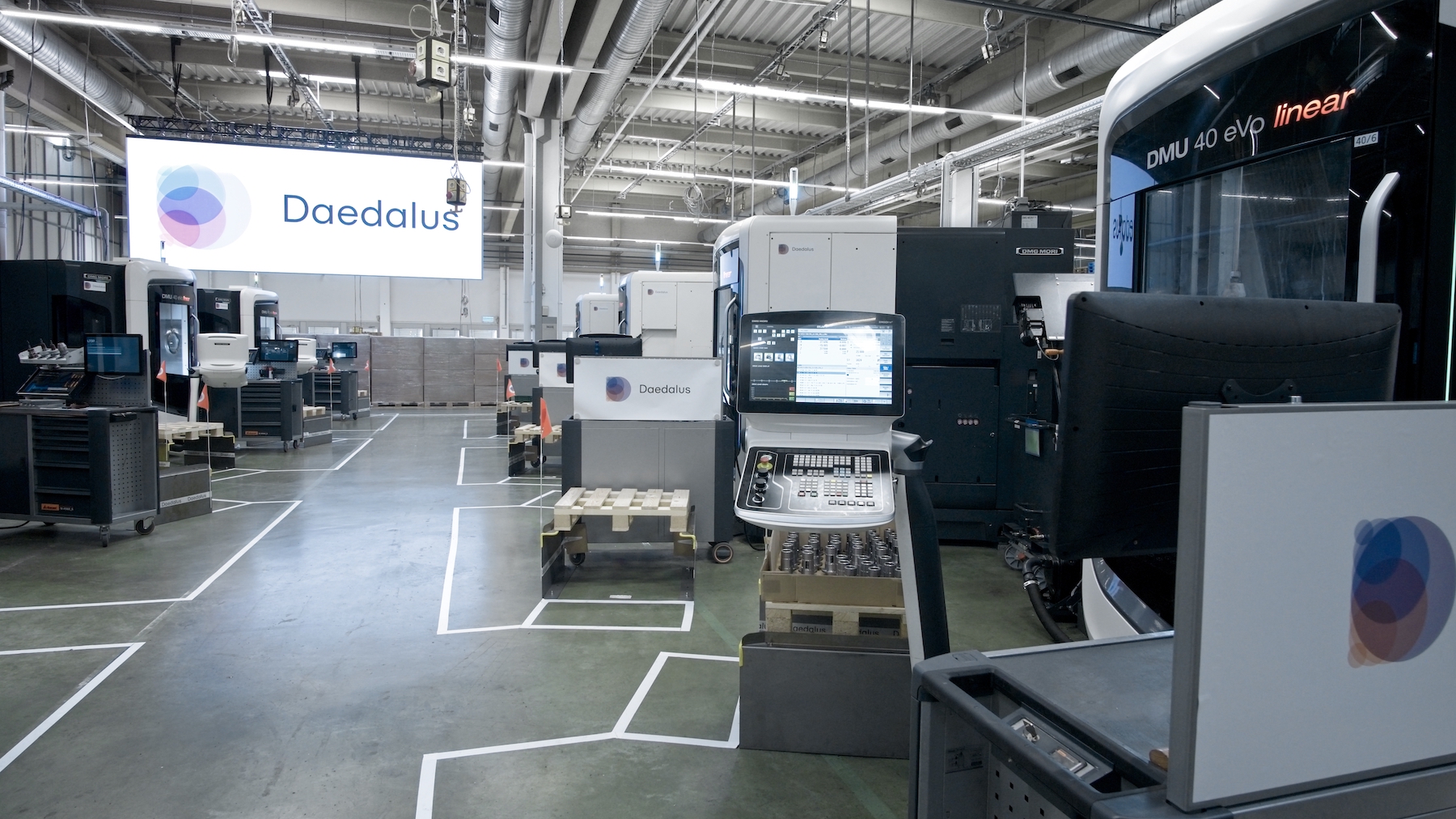
Listen now
When we built our thesis on AI applications within the Convergence of Physical and Digital, we were excited about how this technology would impact the industrial sector. We laid out some “no-regret opportunities”: companies that are deeply integrated within the industrial tech stack, with access to a bespoke data set, experimenting with modern AI to improve workflows in a large market. Since 2020, the whole team NGP has been closely following the development of Manufacturing Tech and we are excited that we have made our first investment in the category.
Today, we are thrilled to announce that we have backed Jonas, CEO and Co-founder, and the whole team at Daedalus by leading their $21M Series A together with existing investors Addition and Khosla Ventures. Daedalus is building the AI-powered factory of the future so that their customers can source precision parts reliably and at scale.
From thesis to reality
Since day one, we have been aligned with Daedalus’ mission to leverage the modern technology toolkit to disrupt a massive industry in the physical supply chain. We were extremely impressed with the milestones that this ambitious team from Karlsruhe, Germany, have achieved in less than 18 months of commercial operations. The enthusiasm to change the world with technology goes way back to when Jonas moved to Silicon Valley and joined Open AI as one of their first employees. The transformative potential of AI, however, inspired him to return home and tackle an intricate problem that had, until then, not been cracked yet.
Cracking the massive market of outsourced precision parts manufacturing
Precision manufacturing serves as the bedrock in the supply chain of nearly all manufacturers of physical products. In Europe alone, machine shops generate an annual turnover of over $130 billion. From wind turbines and rocket engines to cars and life-saving medical devices, manufacturers across the world rely on machine shops’ operations to achieve the exact specifications and tight tolerances of key high-value, complex parts. Many of these parts are produced by CNC machines, where computerized control systems guide the process of cutting and shaping materials with versatility, efficiency, and high repeatability.
What most people don’t know is that the machine in a traditional machine shop is running on average only 20% of the time (!). In the remaining 80%, the team is translating the complex part design into machine-readable instructions, solving problems emerging from operations, or other non-value-adding operations. Plus, many companies don’t have enough personnel to operate shops 24/7. Processes cannot be easily automated as they are iterative and experimental, requiring checks and adjustments at every stage. In the end, operations are inefficient and rely on the knowledge of experienced machinists to manually bring new parts into production.
Another problem is the shrinking supply of experienced machinists who are reaching retirement age and leaving a gap that is not being replaced by newcomers. Adding to the complexity, the market is extremely fragmented, with >80% of the supply being businesses with 10 employees or fewer. While many of these businesses would like to scale, they lack the dataset and technology layer needed to build the necessary automation – creating perfect market conditions for a savvy startup to come in.
How Daedalus is building the world’s most efficient factory
Daedalus fills the unmet growing demand for precision parts in Europe by operating efficient hardware-agnostic CNC factories controlled and operated by their Manufacturing AI Platform. Following multiple disruptions in supply chain, Enterprises are looking for local alternatives that allow for shorter lead times and at the same time meet the competitive prices from Asia. We believe Daedalus has the winning recipe:
- Exceptional team: Jonas co-founded and led software engineering for OpenAI's Robotics team, where among other groundbreaking research, he trained a human-like robot hand to solve the Rubik's cube and pushed the boundaries of what machines can do. His experience puts him in a perfect position to execute this opportunity together with a highly motivated, execution-focused team of software and manufacturing experts from KIT (Karlsruhe Institute of Technology) and across Europe.
- Vertically integrated software-driven approach: Moving the entire production process into a software-driven model enables Daedalus to enhance efficiency across every aspect of the business. At Daedalus, all physical & digital workflows, from quoting and production planning to quality control, are orchestrated by their software (and in some parts even operated by robots), preventing human error.
- AI Foundation: End-to-end integrated data interfaces and process control allows Daedalus to accumulate highly proprietary datasets necessary for fine-tuning use case-specific models. Hence, they can embed AI in a variety of tasks which allows them to both scale the portfolio of parts faster and reduce the required skill level for precision part production from years to months. It allows them to offer competitive prices and shorter lead times.
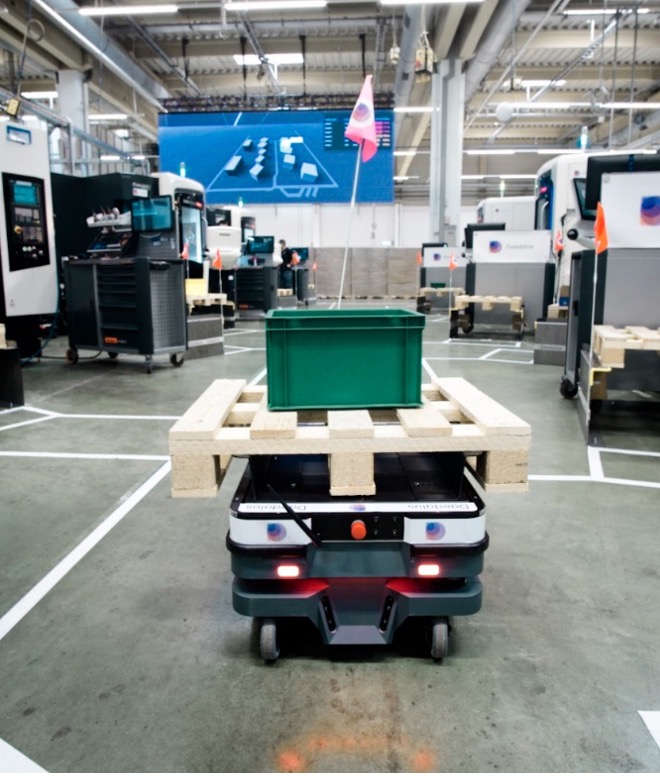
We witnessed first-hand how Daedalus’ model drives value to leading companies in sectors such as semiconductor, medical, energy, e-mobility and defense. Beyond quality, the team is laser-focused on providing service levels that are unprecedented in the industry. Reliable deliveries, real-time progress updates, and digital traceability of each part are just the beginning of what can be done in a software-orchestrated shopfloor.
Kudos to Daedalus' team for building this great company, and a warm welcome to the NGP Capital portfolio!
If you share our enthusiasm and want to join Daedalus’ mission, they are hiring!